Remanufactured Safety Valves
New and Remanufactured Safety Valves
We have decades of experience rebuilding safety valves and pressure relief valves that are tested and certified in our VR facility to factory specifications.
Flotech has VR certification from the National Board of Boiler and Pressure Inspectors in every location. Our trained valve technicians use current manufaturer’s specifications to repair, set, and certify safety and relief valves at your plant in line or at our facilities. We certify both ASME Section I and VIII code stamped safety valves.
We maintain a huge inventory of remanufactured valves, ready to ship with a moments notice. These valves reduce customer downtime and save money. We provide a 100% guarantee and one year warranty.
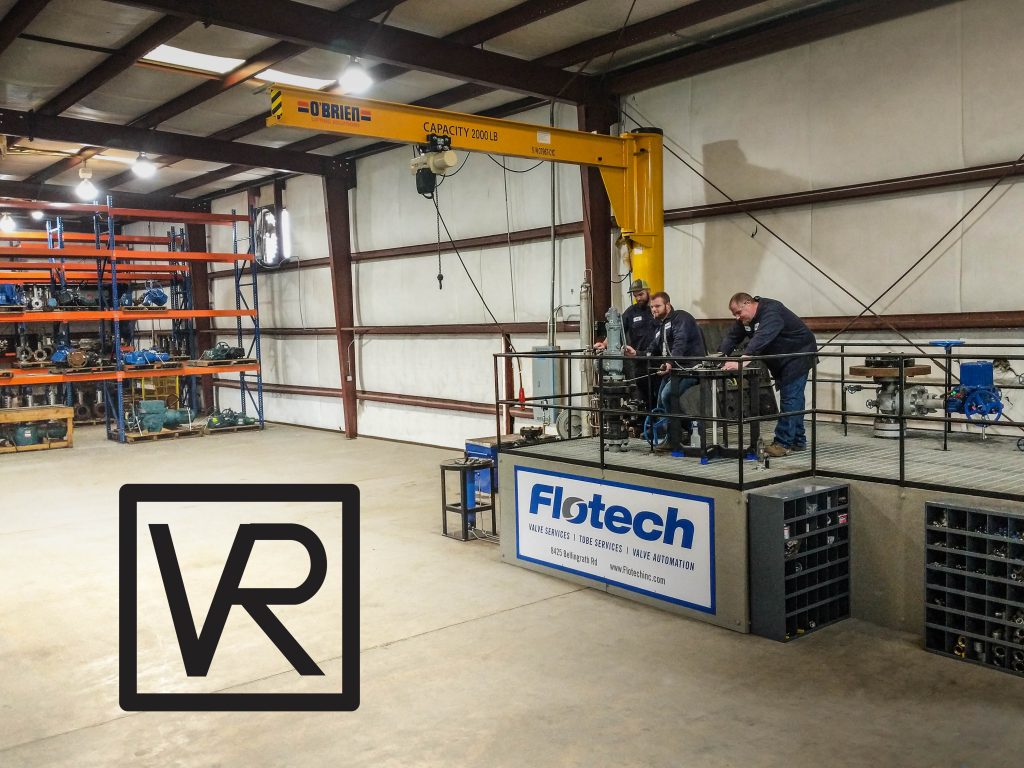
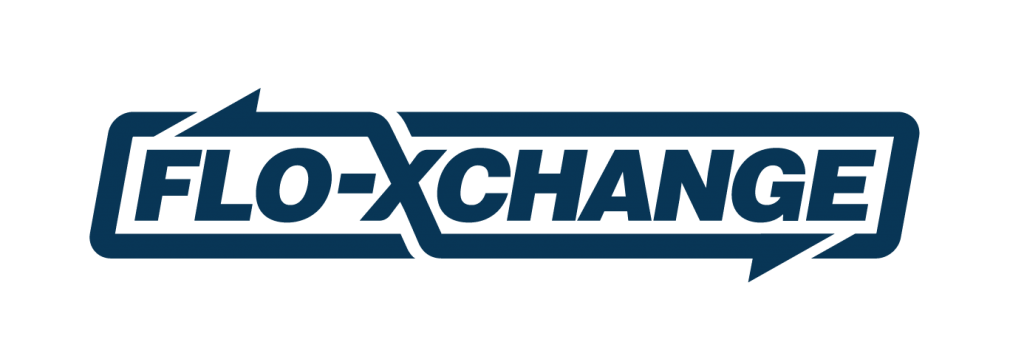
SRV Exchange Program
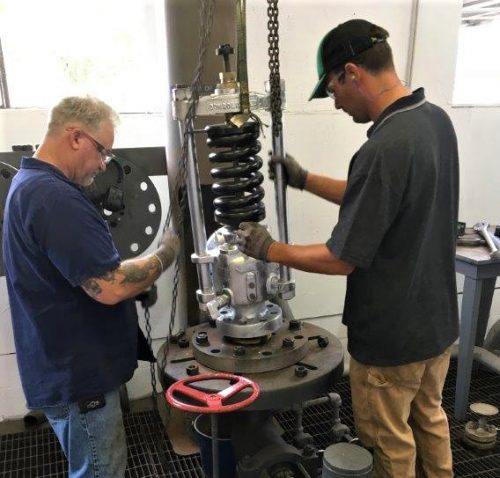
Customers that need a quick turnaround have the option of exchanging their used safety relief valve for one of our rebuilt certified valves. This allows us to deliver a new remanufactured valve immediately and add the old valve to our repair schedule so it is available during the next planned outage.
Flotech will manage the whole process, removing the old valve, replacing it with a rebuilt valve to exacting specifications, repairing the exchanged valve and placing it in storage.
Safety Valve Testing and Repair On Site
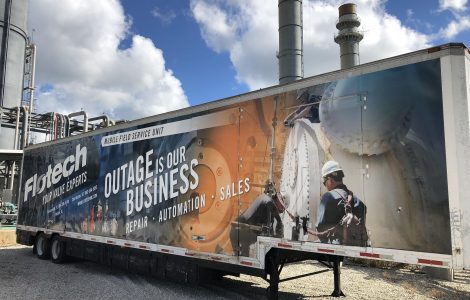
Flotech has trained valve technicans and a mobile valve shop that can deliver testing and repair at your plant. Our field service crews have the latest portable safety valve testing systems developed to test safety valves in position. Flotech uses portable testing equipment to verify the set pressure of safety and safety relief valves in-line, without having to shut down a system or unit. By applying force to the valve spindle, coupled with system pressure, and a “true” effective area, specifications are acquired, processed, stored, and printed.
- Test safety valves while in position, under a full load.
- Unsurpassed accuracy, reliability and safety, with consistently reproducible results.
- Eliminates the possibility of human error throughout every stage of operation.
In- line testing reduces downtime, eliminating the time to remove the valves and send them to our facility.
Quality Assurance Program and VIP
Our quality assurance program monitors every step in the process and ensures these valves function the same as new from the manufacturer.
- Every valve receives a thorough inspection and documentation
- Each part is calibrated and evaluated.
- Replacement parts are to the exact manufacturer’s specifications.
- Every valve is tagged with a barcode and all test results are store online in our VIP- Valve in formation Portal, available to our customers at no charge, 24 hours a day- every day.
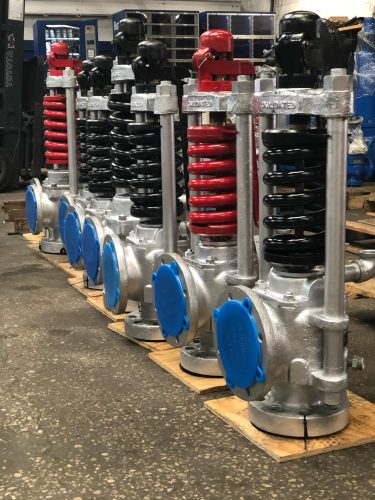